Si-SiC saldato per diffusione
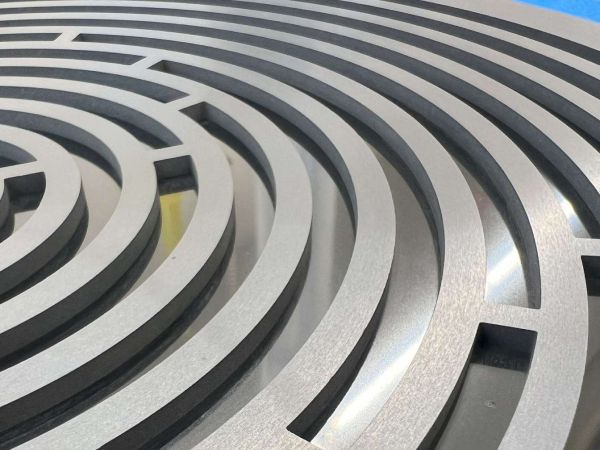
Prodotto | Si-SiC saldato per diffusione |
---|---|
Materiale | Si-SiC |
Metodo di elaborazione | Si-SiC saldato per diffusione |
Dimensione | φ300 |
Applicazione | Il processo di saldatura per diffusione che stiamo sviluppando può unire elementi di diverse forme senza l’uso di materiali intermedi. L’attrattiva di questa tecnologia risiede nel fatto che può creare forme difficili da lavorare meccanicamente, mantenendo nel contempo le caratteristiche del materiale di base. Questa tecnologia rende possibile combinare caratteristiche uniche in una singola struttura attraverso (1) forme di fori profondi, (2) canali di flusso interni, (3) aggiunta o divisione di canali di flusso, ecc., pur mantenendo le stesse dimensioni delle parti convenzionali. Questa tecnologia contribuisce al raggiungimento di forme complesse e multifunzionali richieste per diverse applicazioni. |
Descrizione | ■ Immagine della forma prima dell’unione * Dimensioni esterne: φ300 ① Strato scanalato Lavorazione di una scanalatura come un foro laterale (290 mm nel punto più profondo) (Si presume che sia di 290 mm nel punto più profondo) ② Strato di copertura Copertura dello strato scanalato ③ Strato di fessura Fessura da utilizzare come scanalatura dopo la saldatura
■ Illustrazione della forma dopo la saldatura *Alcune sezioni trasversali sono mostrate per rivelare il foro profondo.
■ Immagine esterna del campione reale ・ Scanalatura È possibile eseguire lavori aggiuntivi dopo l’unione
・Foro laterale * Viene inserito un tubicino di diametro 0,65 mm x lunghezza 300 mm. (Stessa lunghezza dell’immagine sopra) *Possibilità di creare un foro lungo
■ Illustrazione del prodotto finale sviluppato Inoltre, unendo il materiale del coperchio, il percorso di flusso può essere formato liberamente.
|